Pet Food Factory
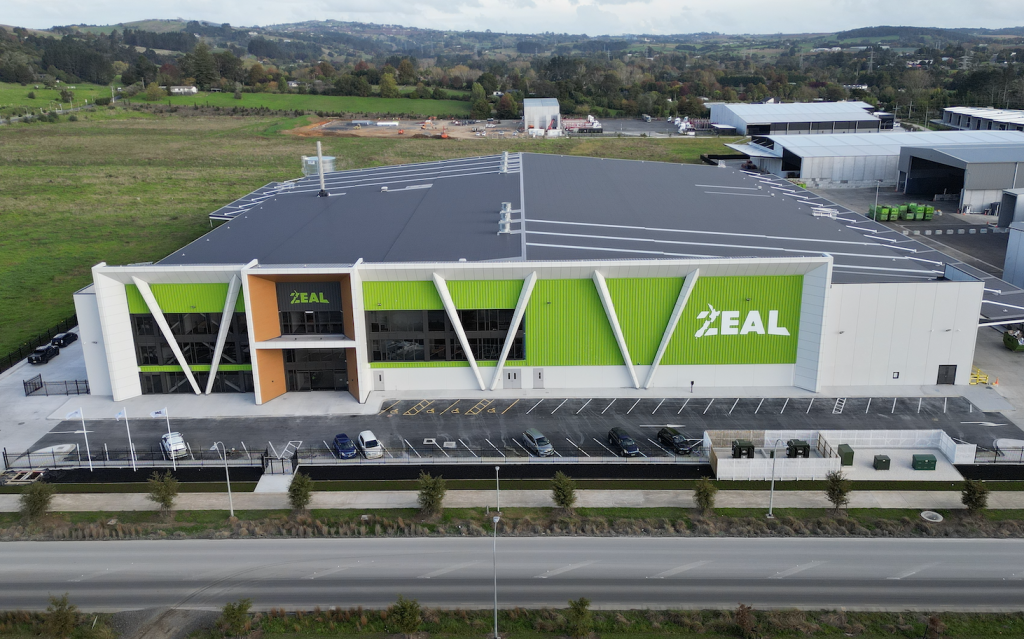
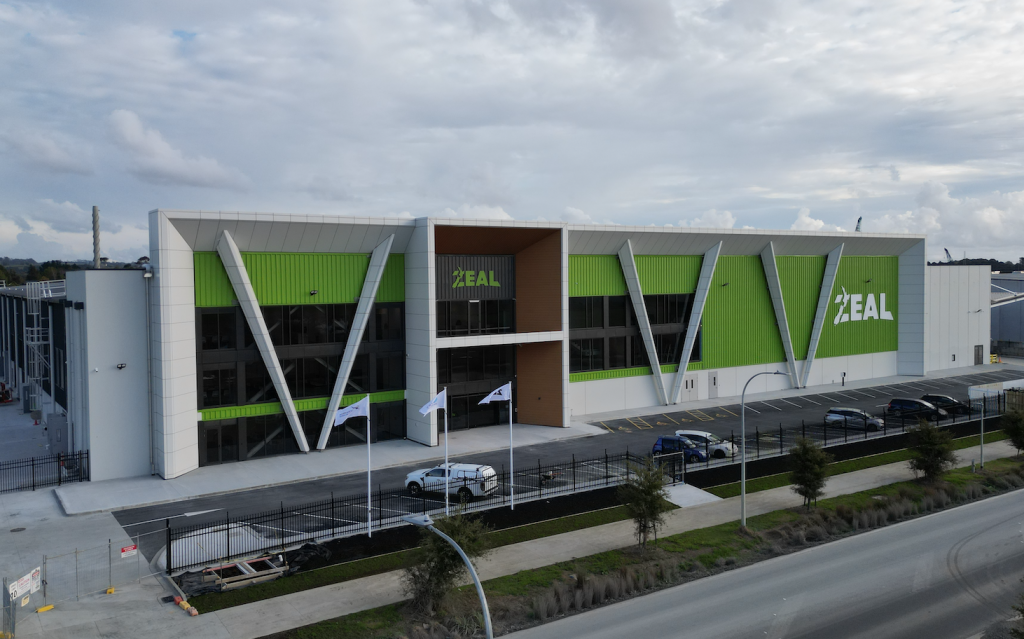
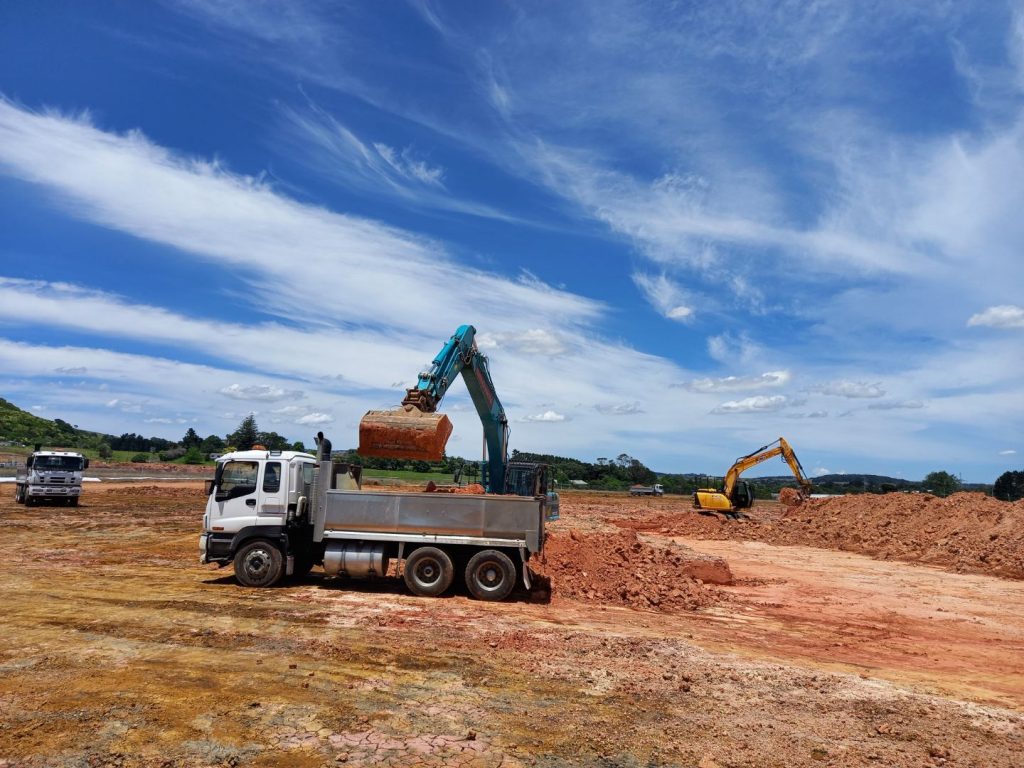
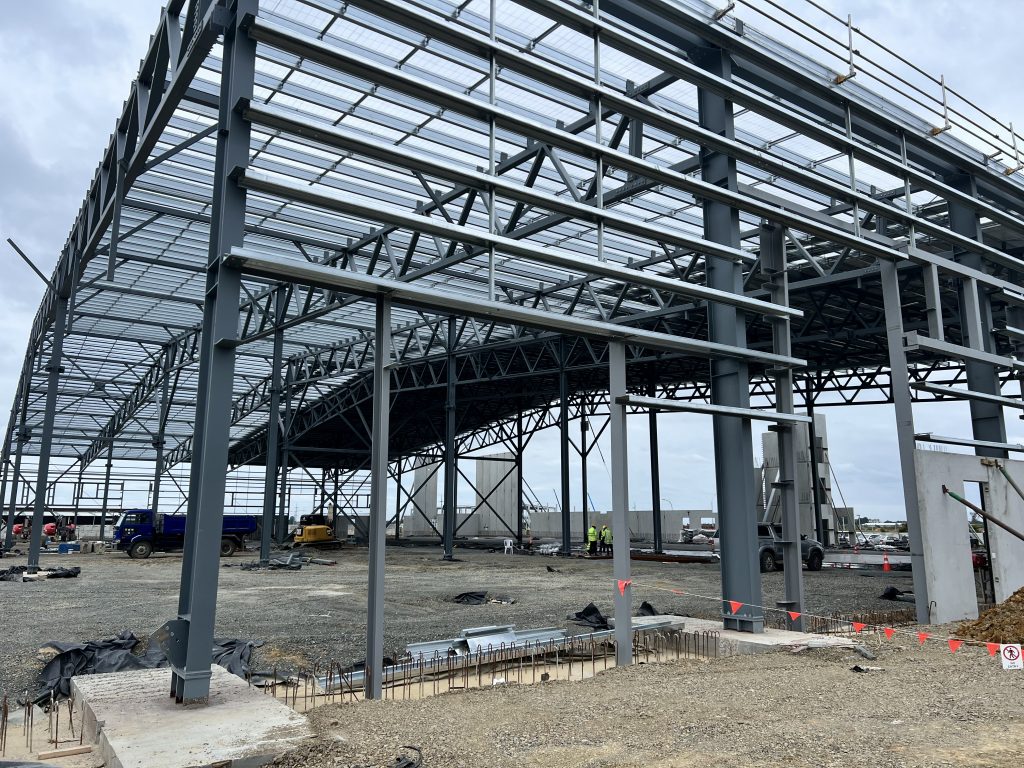
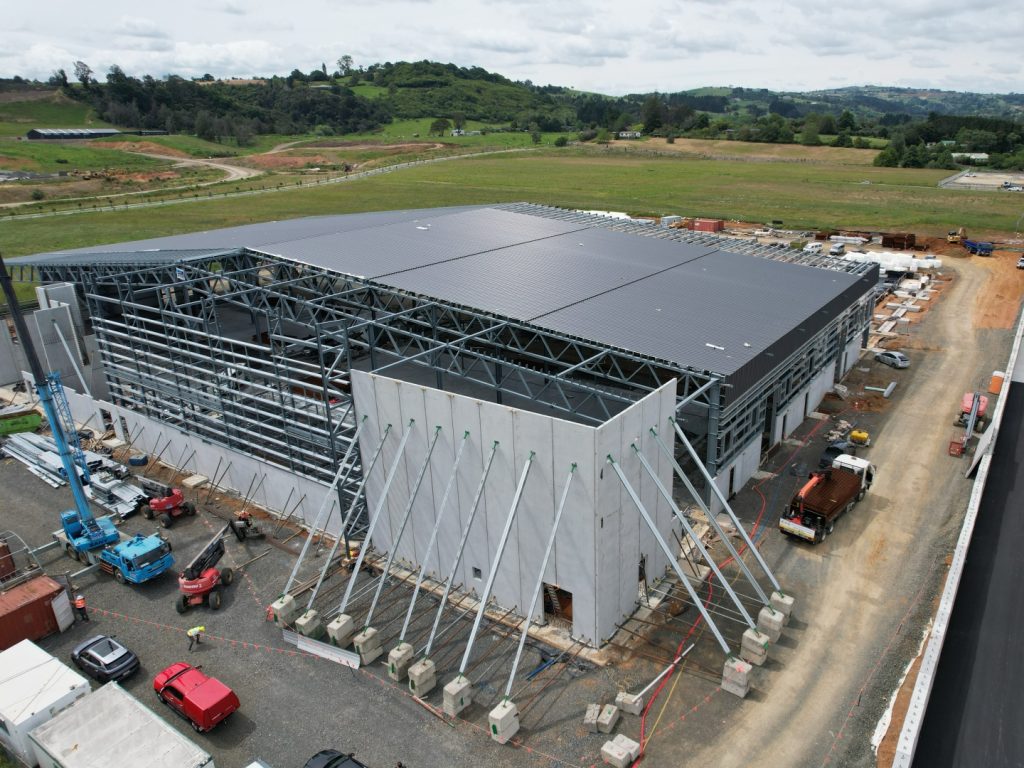
Sector:
Commercial + Industrial
Client:
The Natural Pet Treat Company Limited
Prostone Team:
Peter Niu – Project Lead
Frank Xu – Technical Advisor
Red Zhou – Project Management Lead
Steve Zhou – Project Manager
Raymond Kwan – Quantity Surveyor Lead
Silvia Sun – Quantity Surveyor
Emily Yu – Quantity Surveyor
Project Summary:
This project entails the construction of a state-of-the-art, multi-functional facility designed to support an automated production line, covering a total site area of 25,000 square meters, with a building footprint of 15,500 square meters. The scale and complexity of the build are reflected in the extensive use of high-quality materials and precision engineering.
The project utilizes 9,000 cubic meters of concrete, 2,150 square meters of precast panels, and 1,400 tons of structural steel to ensure durability and structural integrity. The roofing and cladding system spans 16,000 square meters of metal, complemented by 1,000 square meters of sleek aluminium and glass façades for a modern aesthetic.
Interior spaces are safeguarded with 7,500 square meters of fire-resistant wall panels, enhancing safety and compliance with stringent fire regulations. The project also integrates advanced access solutions, including 129 high-speed roller shutters, steel-clad doors, and fire-rated doors, to ensure smooth operation and secure access. With over 100,000 meters of timber and more than 300,000 meters of ducts, pipelines, and electrical cables, the facility is engineered for efficiency and sustainability.
Every element of this development underscores a commitment to innovative design, robust construction, and superior performance, setting a benchmark for future industrial projects.
Prostone Role:
Prostone Consulting played a pivotal role in the Pet Food Factory project, acting as both the Project Manager and Professional Quantity Surveyor (PQS). From project inception to completion, Prostone led the coordination of complex construction activities, ensuring seamless collaboration among key stakeholders and maintaining a strong focus on delivering within budget and timeline constraints.
Collaborating seamlessly with Babbage for design and consenting management, Prostone managed tendering process closely with the client and all the tenderers to identify resource shortage issues on the market. We persuaded the client to engage the main contractor on the P & G / Margin basis, and then worked with the main contractor (Orient Construction Ltd) to secure the key subcontractors very quickly, the procurement process was transparent and efficient, which enable the project team to overcome the material and skill shortage on the construction market.
During the construction, Prostone’s team of project managers, QSs and design managers proactively worked together with the client, main and subcontractors, ensured project objectives of time cost quality and safety being clear and understood among all stakeholders, regular and simplified project management mechanism is in place, issues and conflicts were dealt with professionally.
Prostone was able to deliver the project on time for every stage of the project, including due diligence, Resource Consent design and approval, Building Consent design and approval, tender process and construction commencement phase, and then finally handing over the building to the client so they could start the installation of the manufacturing equipment.